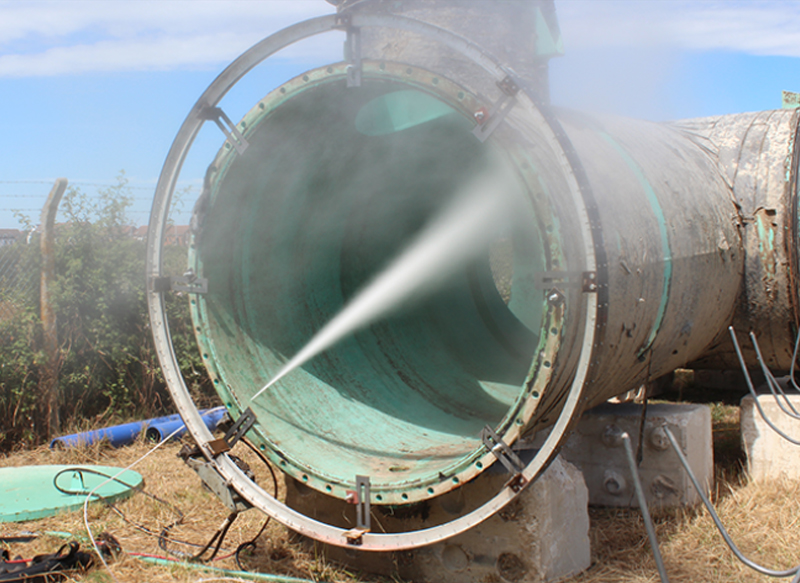
Hydro-Abrasive Cold Cutting
Hydro-abrasive cold cutting services are specialized procedures used in various industries to precisely cut or remove materials in a controlled and efficient manner. This innovative technique combines the power of high-pressure water jets with abrasive materials, such as garnet or aluminum oxide, to cut through a wide range of materials, including metal, concrete, and composites. In this article, we will delve into the importance, methods, and benefits of hydro-abrasive cold cutting services.
Importance of Hydro-Abrasive Cold Cutting:
- Precision Cutting: Hydro-abrasive cold cutting is known for its exceptional precision. It allows for intricate and accurate cuts, making it suitable for industries where precision is critical, such as aerospace and automotive.
- Reduced Heat-Affected Zones: Unlike traditional heat-based cutting methods like plasma or oxy-fuel cutting, hydro-abrasive cutting generates minimal heat, reducing the risk of heat-induced deformations or changes in material properties.
- Versatility: Hydro-abrasive cold cutting can be used on a wide variety of materials, from metals to concrete and ceramics, making it a versatile choice for industries with diverse cutting needs.
- Minimized Dust and Fumes: The process generates minimal dust and fumes, making it a cleaner and safer option, especially in enclosed or sensitive environments.
Methods of Hydro-Abrasive Cold Cutting:
Hydro-abrasive cold cutting involves the use of a high-pressure water jet combined with an abrasive material. The cutting process typically follows these steps:
- Water Jet Generation: High-pressure water, typically pressurized to several thousand psi, is generated by specialized pumps.
- Abrasive Injection: Abrasive material, such as garnet or aluminum oxide, is mixed with the high-pressure water in a mixing chamber.
- Nozzle and Cutting: The abrasive-laden water is forced through a specially designed nozzle at supersonic speeds. As the jet exits the nozzle, it carries the abrasive particles with it, effectively cutting through the target material.
- Controlled Movement: The cutting process is controlled using computer-aided systems, allowing for precise and repeatable cuts.
Benefits of Hydro-Abrasive Cold Cutting Services:
- Precision and Accuracy: Hydro-abrasive cold cutting excels in delivering precise and accurate cuts, making it ideal for applications where tolerances are critical.
- No Heat-Affected Zones: The process generates minimal heat, reducing the risk of warping, cracking, or changes in material properties, especially in heat-sensitive materials.
- Versatility: It can be used on a wide range of materials, including metals, ceramics, composites, and concrete.
- Minimal Environmental Impact: Hydro-abrasive cold cutting is environmentally friendly as it produces minimal dust, fumes, and waste compared to other cutting methods.
- Safety: It is a safe cutting method, particularly in environments where fire hazards are a concern due to its cold cutting nature.
Applications of Hydro-Abrasive Cold Cutting Services:
- Aerospace: Hydro-abrasive cold cutting is commonly used in the aerospace industry for precision cutting of composite materials used in aircraft manufacturing.
- Automotive: It is used in the automotive industry for cutting metal parts, such as chassis components and exhaust systems.
- Shipbuilding: Hydro-abrasive cutting is valuable in shipbuilding for cutting thick metal plates and removing corroded sections of ships.
- Construction: It is used in construction for precision cutting of concrete and masonry materials.
- Oil and Gas: Hydro-abrasive cold cutting is employed in the oil and gas industry for pipe cutting, decommissioning of offshore structures, and maintenance of pipelines.
Future Trends in Hydro-Abrasive Cold Cutting Services:
- Automation and Robotics: The use of robotics and automation is expected to increase, allowing for even greater precision and efficiency in hydro-abrasive cold cutting.
- Advanced Materials: As industries continue to adopt advanced materials, hydro-abrasive cold cutting methods will need to adapt to handle these new materials effectively.
- Environmental Sustainability: There will likely be a greater focus on environmentally sustainable cutting methods, including the development of eco-friendly abrasive materials and recycling of water used in the process.
- In-Field Applications: Advancements in portable hydro-abrasive cold cutting systems will enable on-site cutting for industries such as construction and maintenance.
In conclusion, hydro-abrasive cold cutting services provide a versatile, precise, and environmentally friendly method for cutting and removing materials across various industries. As technology continues to advance and industries seek cleaner, more efficient cutting solutions, hydro-abrasive cold cutting is likely to play an increasingly vital role in shaping the future of material processing and manufacturing.