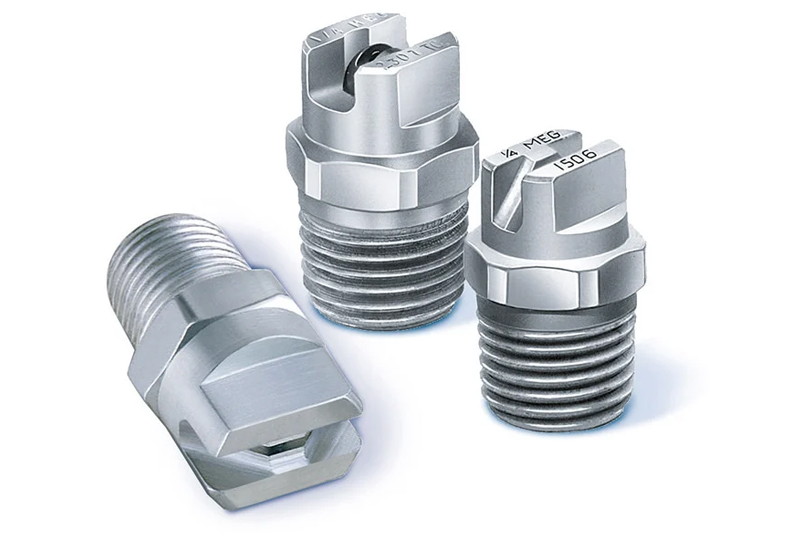
High Pressure Nozzles
High-pressure nozzles are critical components used in a wide range of industrial applications, where precision and controlled fluid delivery are essential. These nozzles are designed to produce intense, focused streams of fluid, such as water or other liquids, at significantly higher pressures than standard nozzles. High-pressure nozzles find application in various industries, from cleaning and cutting to surface preparation and firefighting. In this article, we will explore the importance, types, applications, methods, and benefits of high-pressure nozzles.
Importance of High-Pressure Nozzles:
High-pressure nozzles play a crucial role in several industries for several reasons:
-
Precision: They deliver fluids at exceptionally high velocities with precision, making them suitable for tasks requiring accurate and controlled fluid flow.
-
Efficiency: High-pressure nozzles are known for their ability to break down tough materials, clean surfaces more thoroughly, and reduce water or fluid consumption compared to conventional nozzles.
-
Versatility: These nozzles can be customized for different applications, including cleaning, cutting, coating, cooling, and fire suppression, among others.
-
Safety: High-pressure nozzles are used in environments where safety is paramount, such as industrial equipment cleaning, high-precision cutting, and firefighting.
Types of High-Pressure Nozzles:
High-pressure nozzles come in various types, each designed for specific applications:
-
Flat Fan Nozzles: These produce a flat, fan-shaped spray pattern and are often used for cleaning, surface preparation, and cooling applications.
-
Full Cone Nozzles: Full cone nozzles produce a cone-shaped spray pattern and are commonly used in applications like spray drying and humidification.
-
Hollow Cone Nozzles: Hollow cone nozzles produce a hollow, cone-shaped spray pattern and are used in applications where uniform coverage is essential, such as cooling towers.
-
Solid Stream Nozzles: These nozzles produce a single, focused stream of fluid and are often used in cutting, drilling, and descaling applications.
-
Variable Spray Angle Nozzles: These nozzles allow the adjustment of the spray angle, making them versatile for different applications.
Applications of High-Pressure Nozzles:
High-pressure nozzles find application across a wide range of industries and tasks:
-
Cleaning: High-pressure nozzles are extensively used in industrial and commercial cleaning for tasks like pressure washing, surface preparation, and equipment cleaning.
-
Cutting: Waterjet cutting systems employ high-pressure nozzles to accurately cut a variety of materials, including metals, plastics, and composites.
-
Firefighting: High-pressure nozzles are used in firefighting equipment to deliver water or firefighting foam at high velocities to suppress fires.
-
Coating: In the coating industry, high-pressure nozzles are used to apply paint, varnish, and protective coatings onto surfaces, ensuring even coverage and adhesion.
-
Cooling: High-pressure nozzles are employed in cooling systems for industrial processes and equipment to regulate temperature and reduce friction.
-
Surface Preparation: Industries such as automotive and construction use high-pressure nozzles for surface preparation before painting or coating applications.
Methods of High-Pressure Nozzle Operation:
High-pressure nozzles operate following these basic principles:
-
Fluid Supply: A high-pressure pump or hydraulic system pressurizes the fluid, typically water, to the desired pressure level.
-
Nozzle Design: The nozzle’s design determines the spray pattern and flow rate, which can be customized for specific applications.
-
Nozzle Attachment: The high-pressure nozzle is attached to the equipment or system, ensuring proper alignment and secure connection.
-
Activation: The high-pressure fluid is activated, and the nozzle delivers a high-velocity stream or spray pattern as required for the specific task.
Benefits of High-Pressure Nozzles:
-
Precision: High-pressure nozzles offer precise control over fluid delivery, making them ideal for applications requiring accuracy and consistency.
-
Efficiency: They accomplish tasks efficiently, often with reduced resource consumption, whether it’s cleaning, cutting, coating, or cooling.
-
Versatility: High-pressure nozzles can be customized for various applications, making them invaluable in diverse industries.
-
Safety: High-pressure nozzles are designed for safe operation, especially in applications where safety is a primary concern.
-
Cost Savings: Increased efficiency, reduced material waste, and decreased downtime can result in cost savings for businesses using high-pressure nozzles.
Future Trends in High-Pressure Nozzles:
-
Advanced Materials: The development of nozzle materials to enhance durability and performance in extreme conditions.
-
Automation: Greater integration of automation and robotics in nozzle systems, enabling precise and repeatable fluid delivery.
-
Smart Nozzles: The development of smart nozzles equipped with sensors and data monitoring capabilities for real-time feedback and adjustment.
-
Eco-Friendly Solutions: Increasing demand for eco-friendly nozzle designs and materials to minimize environmental impact.
In conclusion, high-pressure nozzles are crucial in industries that require precision, efficiency, and versatility in fluid delivery. As technology advances and industries continue to prioritize safety and sustainability, high-pressure nozzle systems will evolve to meet the changing needs of industrial processes and maintenance.